|
Central Vacuum Ceaning System (CVC)
‘Doctaire’ Sturtevent’ range of centralised vacuum cleaning (CVC) system provides an effective solution where quantities of dust or other material must be regularly removed from one or more floor levels to a central point on a continous basis either for disposal or recycling. Centralised systems VAC Cleaning can be designed into new bulidings or installed in existing buildings. Whichever the option, we provides a comprehensive and after sales service.
A typical centralised Vacuum Cleaning system will include hose connection points in key areas throughout the building, with interconnecting pipe work to couple them to a conveniently sited filtration & turbo exhouster / Power Head unit. Centralised systems are in daily use in applications as diverse as Cement, Iron & Steel, Power Plants cereal producers, ships and foundries. Other specialist applications include many materials that are abrasive, toxic or explosive, where the system helps to protect bothpersonnel and plant.
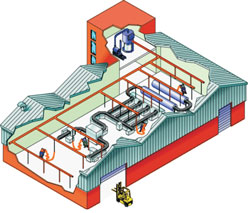
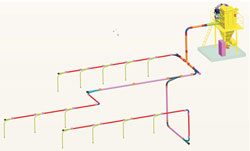
Advantages :
- Efficient
- Durability
- Minimum Maintenance Requirements
- Hygiene, Environment and Legislation Compliance
- Low Labour cost / minimum man power
- Material Claiming
Application :
- Cement Plant
- Iron & Steel Industries
- Graphite & Coal
- Power Plant
- Chemical, Detergent & Textile Industries
|
Four Stage Unique Filtration System
The Mammoth boasts four stages of filtration to fully clean the conveying air and return it to atmosphere without any airborne pollution.

Stage 1
Primary Separation takes place directly into the material collection hopper where the majority of material is removed by the effect of slowing of the conveying air velocity.
Stage 2
Fine dusty material and moisture is drawn at high velocity through a narrow slot into a large chamber where the air slows on entry, depositing any particles to the bottom.
Stage 3
Any remaining dust particles are removed from the air by the fabric filter.
Stage 4
A cartridge filter is employed to protect the Vacuum Pump and subsequently the environment, in the event of damage to the fabric filter. For collection of toxic substances, this final cartridge filter can be replaced by a HEPA filter for added protection.
Options
• Range of sizes from 7.5 to 150kw • Electric, Diesel, LPG engines • Acoustic Enclosure for noise reduction • ATEX Compliant Models • Support Frames, Access and Service Platforms • Truck / trailer mounting • Wide variety and size of Hoppers including self-tipping • Dump, Slide, Rotary Valve Hopper discharge options |
Material Recovery
Continual increases in raw material costs means lower profits from any waste created. The Mammoth provides the opportunity to reclaim spillages and where applicable, return them to the process for reuse. A Primary Interceptor can be installed in the system to collect the material and discharge it onto a reclaim conveyor or silo.
Aiding Compliance with
Environmental Legislation
Removal of spillage, dust and debris using conventional methods has been proved to be both inefficient and costly both in labour and its effect on the environment. The actions of brushing, shovelling or blowing can disturb dust and re-pollute the environment. Collection of dust and debris, by the use of vacuum cleaning, ensures immediate safe collection, eliminating disturbance and allowing for disposal or re-use safely. The Doctaire Mammoth offers the capabilities to cost effectively remove, contain and dispose of dust and debris, including toxic waste, helping owners and operators comply with the increasingly onerous legislation around the world. |
|
|